モーデックが過去に実施したコンサルティング、モデリング、
設計支援の実績の一部を抜粋しています。
シミュレーション活用による
ディレーティング検証
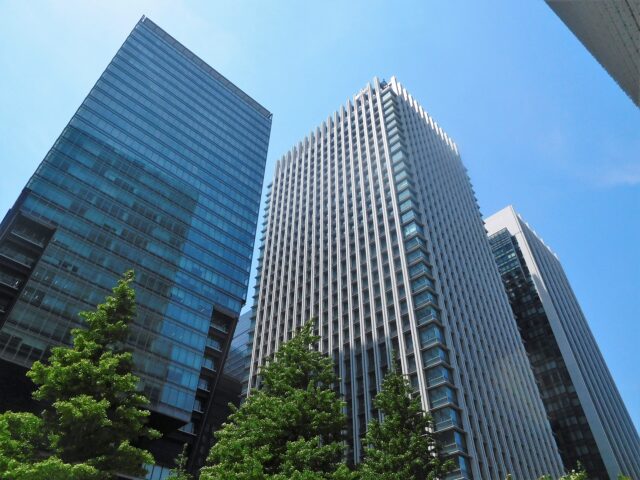
モーデック製品
問題点
部品変更時の検証不足
電子部品の故障確率は右図バスタブ曲線のように、時間と共に上昇しますが、その寿命はアレニウスの法則に従い熱の影響を大きく受けるため、十分に検証する必要があります。通常は設計時に最大定格を保証する試験や、温度上昇試験を行いますが、EOL(部品の製造中止)やValue Engineeringによる代替部品検討時には簡易的な確認で済ませることがあり、検証漏れによる製品リスクを孕んでいました。
<具体例>
- スピード対応の要求により主要SPECのみ確認
- 動特性の差により動作波形やディレーティングに乖離が発生
- 最大定格に対するマージンや発熱量の差により、製品寿命が短くなる
変化点を全て網羅して設計計算・実験を行い判定することが理想ですが、人海戦術では管理漏れやスキル差が課題だったため、SPICEシミュレーションを活用した検証の自動化に取り組みました。
しかしながらシミュレーションに必要な正確なデバイスモデルの入手には課題がありました。そこでメーカから入手できなかったり、精度が不足するものはモーデック社から入手しました。
Model On!サービスでは定期的にモデルが追加され、メーカー製モデルとモーデック製モデルが用意されているので、ワンストップで入手でき、レアなモデルも受託サービスで入手することができました。
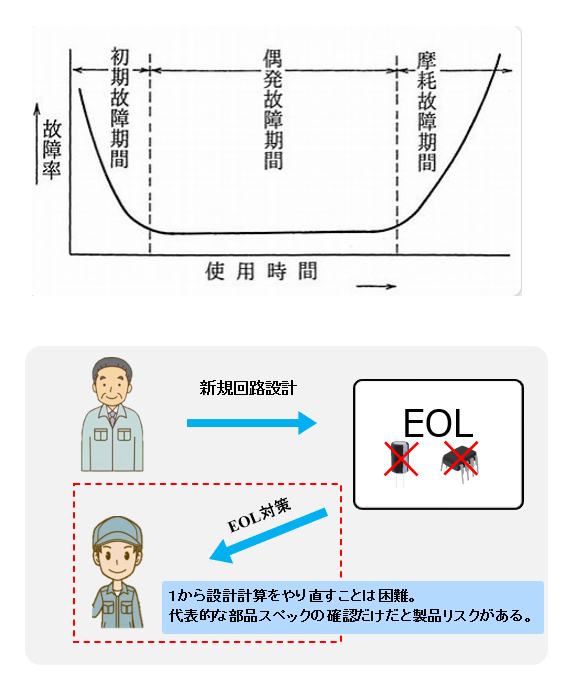
取り組み課題
AC-DC変換回路におけるシミュレーションとディレーティング検証
絶縁型フライバック回路の負荷変動の影響をシミュレーションしました。各ノードの電圧を監視し、実機との相関を確認することで、部品ストレスの影響をシミュレーションで予測しました。
利用したモデル
電源IC、フォトカプラ、シャントレギュレータ、ダイオード | Model On! を通じて入手(データシートに合わせこみ) |
トランス | 受託サービスを通じて入手(測定結果に合わせこみ) |
パッシブ等、その他の部品 | メーカー製モデルを利用 |
結果①
電源解析時のキーポイントである、起動時の電流増加の様子や、負荷変動時の過渡的な影響をシミュレーションで確認し、設計にフィードバックできるようになりました。
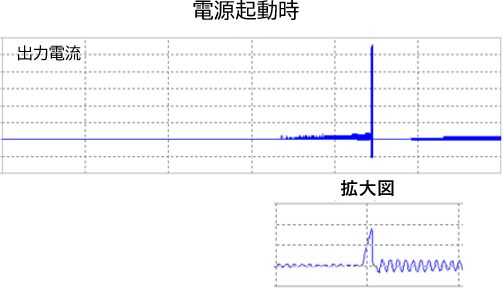
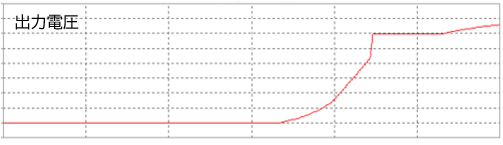
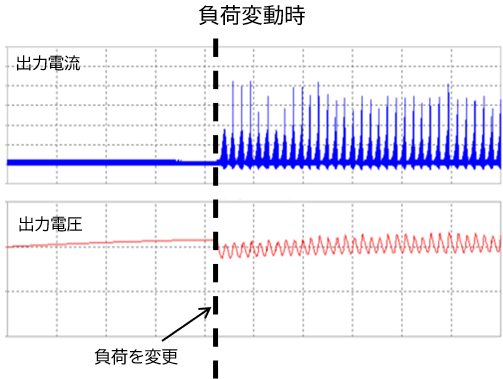
負荷変動時の評価をシミュレーションにより事前に実施できるようになりました。
結果②
CADとシミュレーションを連成した環境を構築することで、ディレーティングを判定するシステムを構築しました。
SPICEで計算した電流と電圧から電力を求め、マクロ処理でディレーティングを計算します。
その結果をユーザ基準と比較することで、OK-NGを判定します。
また消費電力を熱シミュレータへの入力として用いることで、輻射熱の評価も可能です。
今後の課題
■シミュレーションを活用するエンジニアの拡大
- エンジニアが使いやすいように、モデルを集中管理して関係部署で共有化することを目指します。
- 部門ごとにシミュレーションを活用する責任者の設置や社内教育を実施していきます。
■活用アプリケーションの拡大
- 実践的な部品バラツキまで考慮していきます。
- ノイズ解析や対策にまで活用範囲を拡大することを目指します。