モーデックが過去に実施したコンサルティング、モデリング、
設計支援の実績の一部を抜粋しています。
電源設計におけるシミュレーション活用とノウハウの蓄積
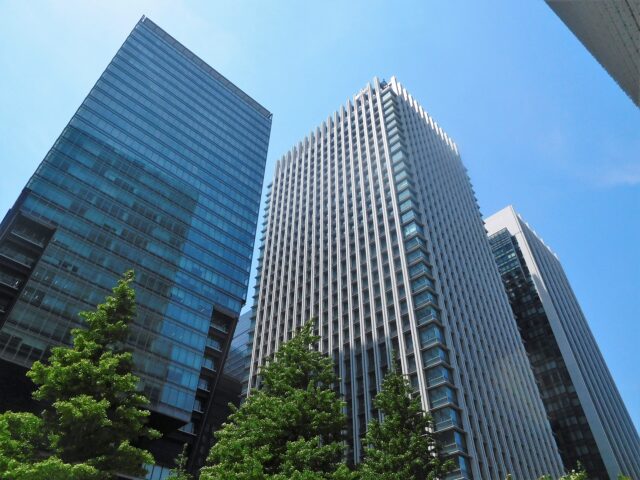
基板の施策回数を減らしたい
モーデック製品
問題点
電源基板設計の自社ノウハウ化と効率化
外部業者に設計を依存していると、電源メーカが撤退した際に設計がやり直しとなり非効率でした。
自社で設計ノウハウを蓄えることで、委託メーカが変わっても回路や部品を流用することが理想ですが、基板設計においてノイズや発熱等の課題があり、試作のやり直しが発生していました。
そこで、回路シミュレーションを利用した設計効率化に取り組みました。
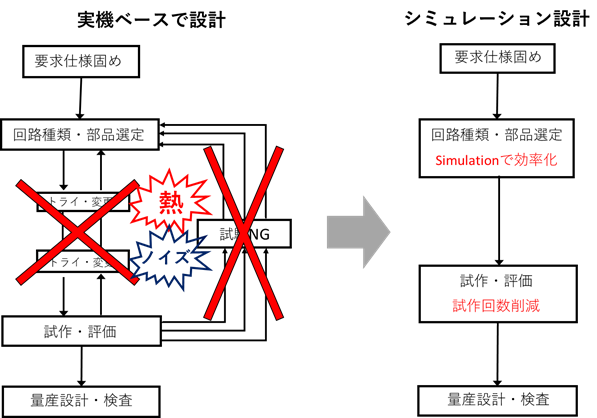
しかしながらシミュレーションに必要な正確なデバイスモデルの入手には課題がありました。
そこでメーカから入手できなかったり、精度が不足するものはモーデック社から入手しました。
デバイス別 モデルの課題
デバイス種類 | 状況 |
---|---|
スイッチングFET | メーカ製モデルと実機波形で差異がある。海外製部品のモデルが手に入らない。 |
電源制御IC | メーカがモデルを提供しておらず手に入らない。 |
フォトカプラ | メーカがモデルを提供しておらず手に入らない。提供されている場合にも精度が不足。 |
トランス | 実機と自作モデルで波形が異なる。また測定値が安定しない。 |
コンデンサ | バイアス依存特性で波形が異なる。 |
取り組み課題
①AC-DCスイッチング電源回路のシミュレーション
最初のStepとして出力電圧の再現や、回路動作の確認を目的とし、正しい型番の部品モデルを揃えてシミュレーションしました。入手できないモデル(図中の赤点線で囲ったもの)はModel On! サービスを利用してデータシートから作られたモデルを入手しました。
結果
・ 実機の挙動をシミュレーションで再現することができました。
・ モーデック社のサポートにより、ブラックボックス化していて動作の理解が困難であった制御ICモデルの理解が進み、
回路全体の理解を深めることに繋がりました。
・ 実機と動作が異なる場合の解析手法のアドバイスにより、原因究明とその解決がスムーズに行えました。
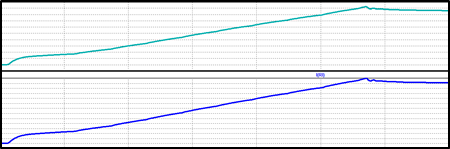
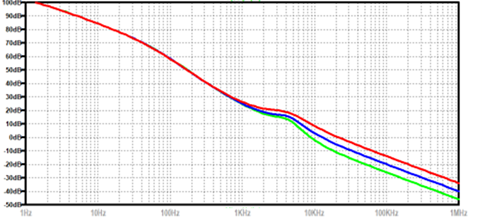
課題のあった部品モデルはModel On! サービスで追加作成することで、解決しました。
②熱やノイズの再現を目的としたシミュレーション精度向上
実機検証において特に課題となるノイズや熱をシミュレーションで再現するため、精度の向上に取り組みました。
そのために必要な精度の高いモデルを、モーデック社に測定とモデル作成を依頼し、入手しました。
利用したモデル
電源制御IC、フォトカプラ、シャントレギュレータ、ダイオード | Model On! を通じて入手(データシートに合わせこみ) |
トランス、MOSFET | 受託サービスを通じて入手(測定結果に合わせこみ) |
パッシブ等、その他の部品 | メーカー製モデルを利用 |
結果
・ノイズシミュレーション
基板やパッケージ等の寄生成分を考慮することにより、電導ノイズの再現において重要なファクターとなるスイッチング時のサージやリンギングをシミュレーションで再現することができました。
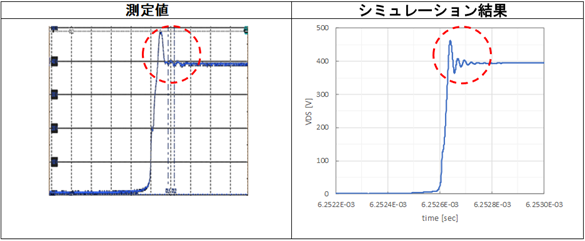
実測値とシミュレーション結果を近づけるための手法についてモーデック社からの適切なアドバイスによりスムーズな解析が実現しました。
プロービングの方法等の測定方法のアドバイスにより、適切な測定結果を得ることができました。
周辺のセラミックコンデンサのモデルや、配線寄生成分の高精度化により、更なる精度向上が見込めます。
・熱シミュレーション
スイッチング損失を少ない誤差で見積ることができるようになり、熱シミュレーションの精度が向上しました。実測値82.2℃に対して、シミュレーション値67.2℃であり、流体や筐体の考慮が必要なため完全には一致しませんが、部品変更時等、相対的な予測に十分活用できる結果です。
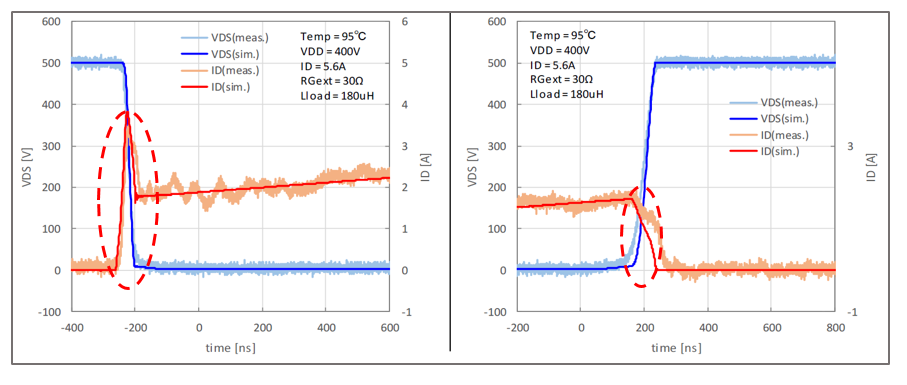
今後の課題
■幅広い部門への展開
・ 今回適応した製品以外の当社製品開発においても、シミュレーション活用を水平展開していきます。
■シミュレーション時間と精度
・ シミュレーション時間を短縮し、より実際の設計に活用しやすい方法を確立する必要があります。
・ 基板の寄生成分も含めたシミュレーションにより、より実測に近い結果を再現することが今後の課題です。